PROJECTS

Manufacturing Order Time Tracking
This QR code on the inventory pick list allows for the ability to track time for a job electronically. This process eliminates …
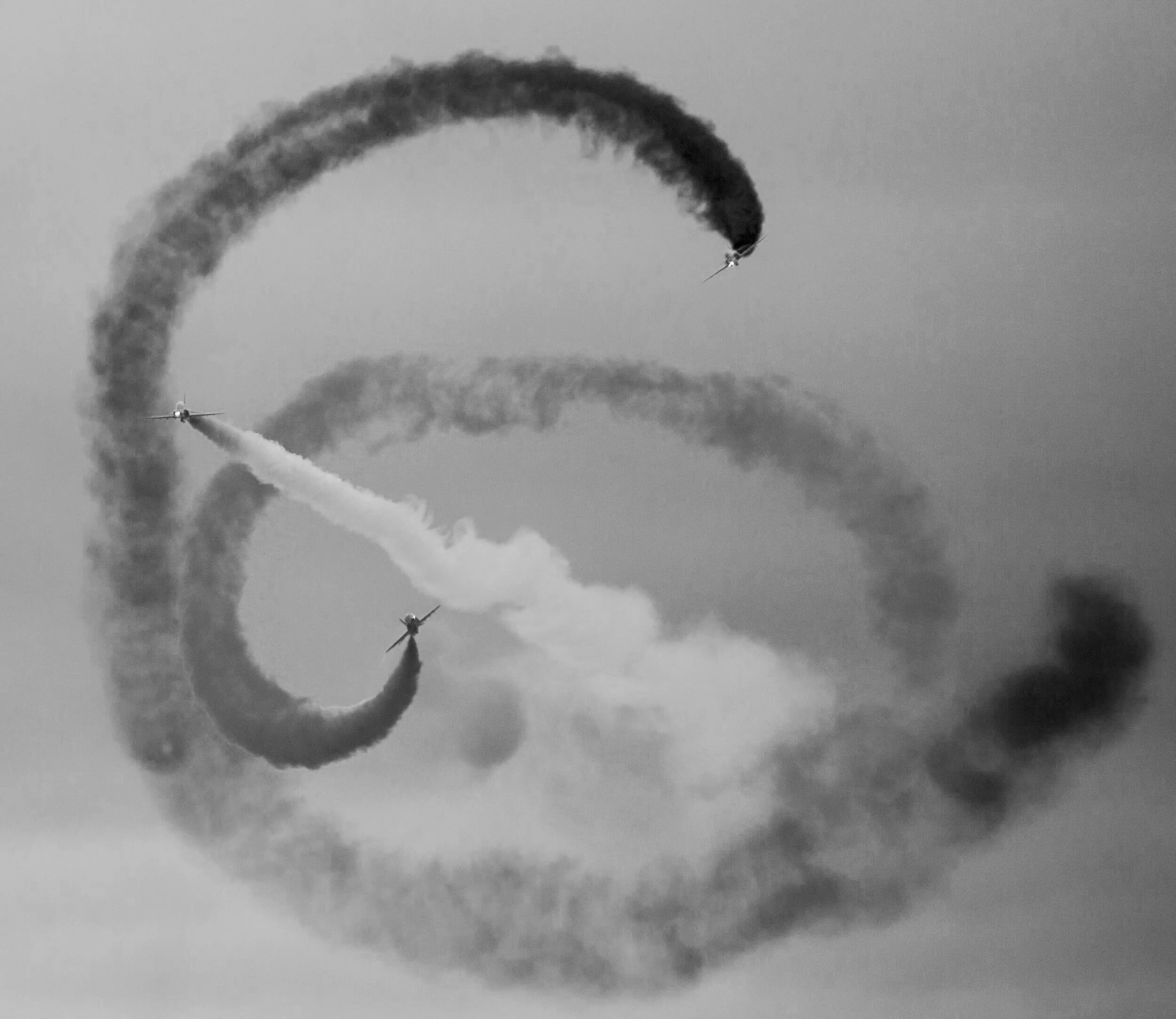
Systems Order Sync
A client has purchased another company through an acquisition and our team was tasked with making the onboarding process as smooth as possible. Through the power of some amazing tools we were able to work from a backlog report that was outputted in excel and keep two disparate, completely different business systems in sync. Each day new orders would go in and would be updated to match what was ordered. This processed saved many hours of duplicate and error prone work in two different systems.
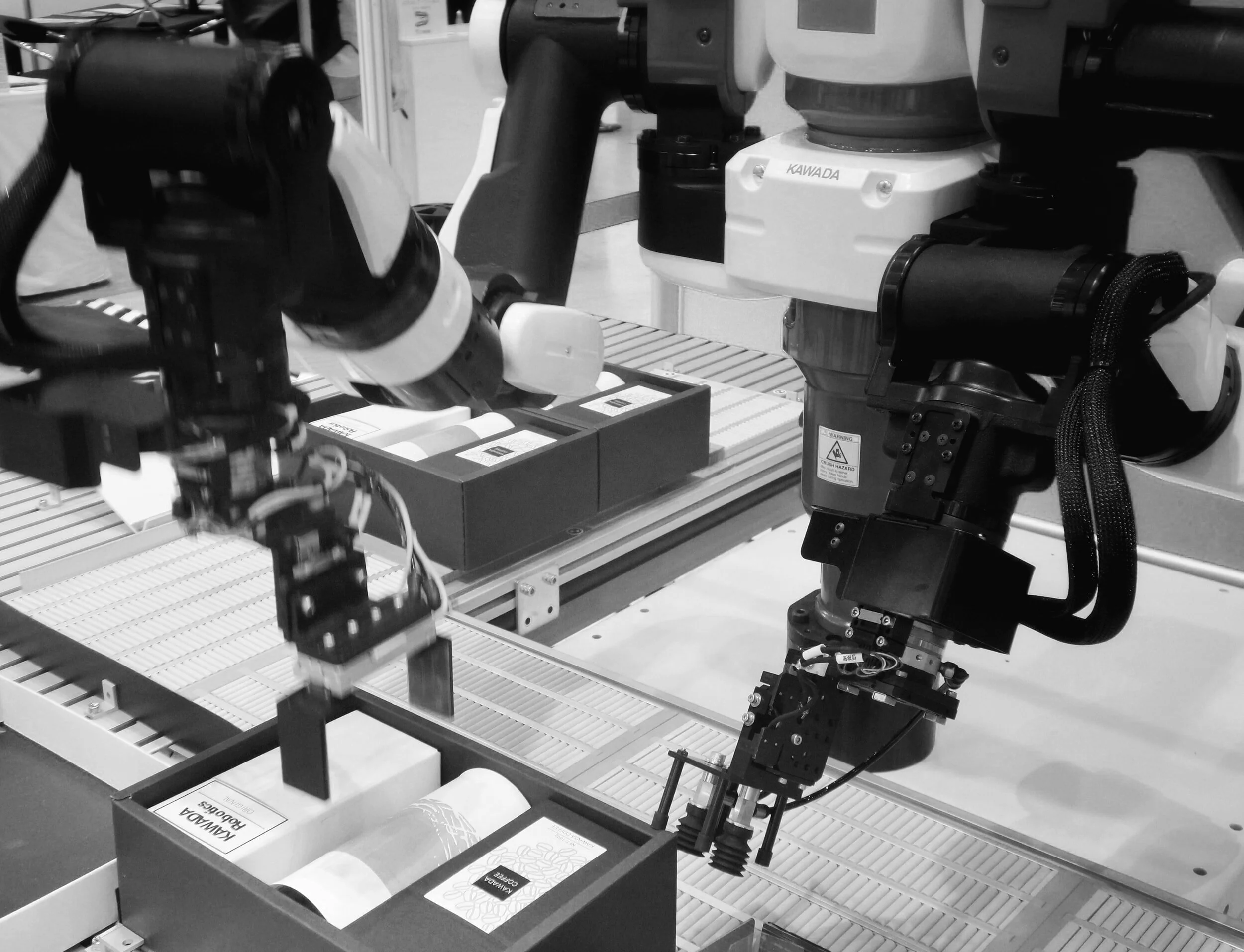
Manufacturing Order Insight
The Manufacturing Order Insight tool we created for this client allows a QR code on the client’s inventory pick list to be scanned and presents several options to the shop floor user. The client can access a PDF drawing of the part that they need and they can view a live inventory pick list of components for a job. Jobs can be moved to or from a department at the click of a button. Our team also worked out proof of concept for PDF drawing markup and 3D model viewing at each department computer.
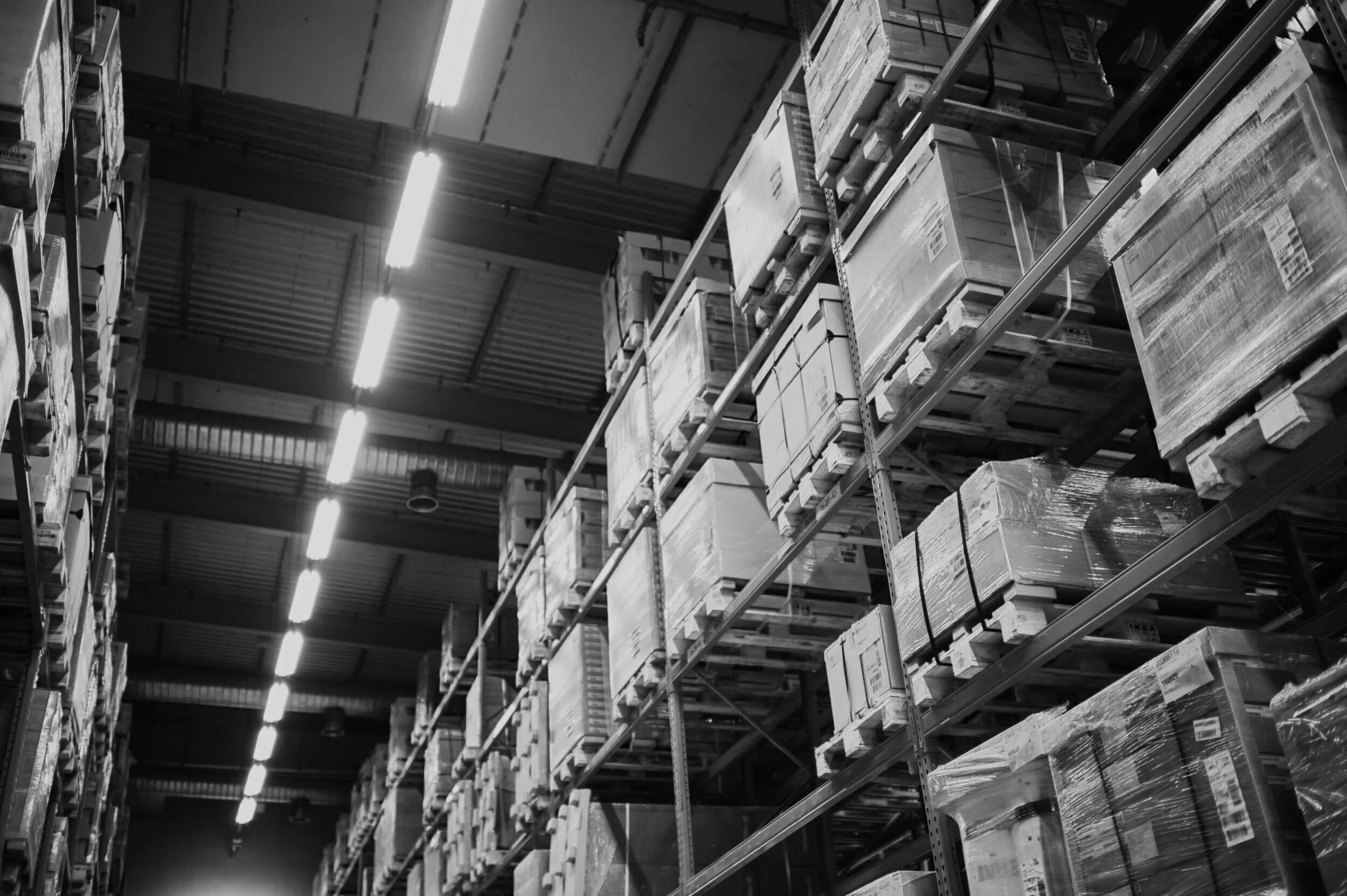
Business System Purchasing Requisition
For this client, we rethought their user interface. We added more safeguards and added better feedback, which resulted in less confusion and less errors. Notifications were added to communicate information to the relevant stakeholders.

Laser Tag (Laser Etching Job & Data Management System)
This system allows the laser operator to simply copy and paste the appropriate data, choose the proper template and laser etched metal ID tags for the client’s products. This system supports all work that runs through the client’s etching laser for ID Tags and other product information necessary for compliance or testing criteria.
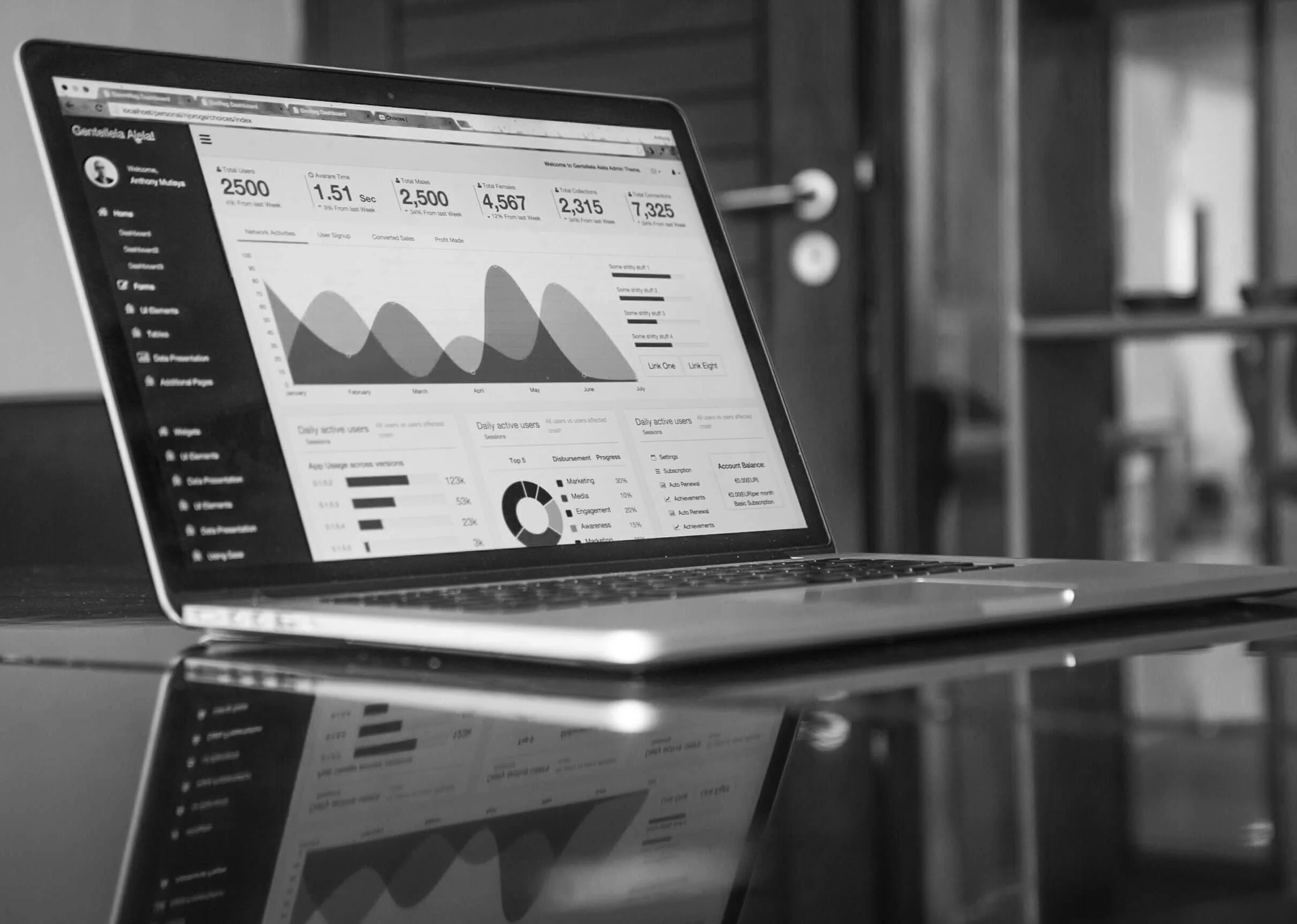
JobDEQ
The pandemic forced this project forward because of the work from home situation. The Job Design Engineer Queue (JobDEQ) allows engineers to manage their work. What was a paper driven process before has been replaced with an interactive, sleek, color-coded system. JobDEQ also gives more information to the engineer, and automates notifications to multiple people in the organization when different events occur. Business system purchase requisitions have also been embedded in this project to significantly smooth the friction of creating a requisition. The JobDEQ also makes parts that have already been ordered for a given job visible in the job detail.
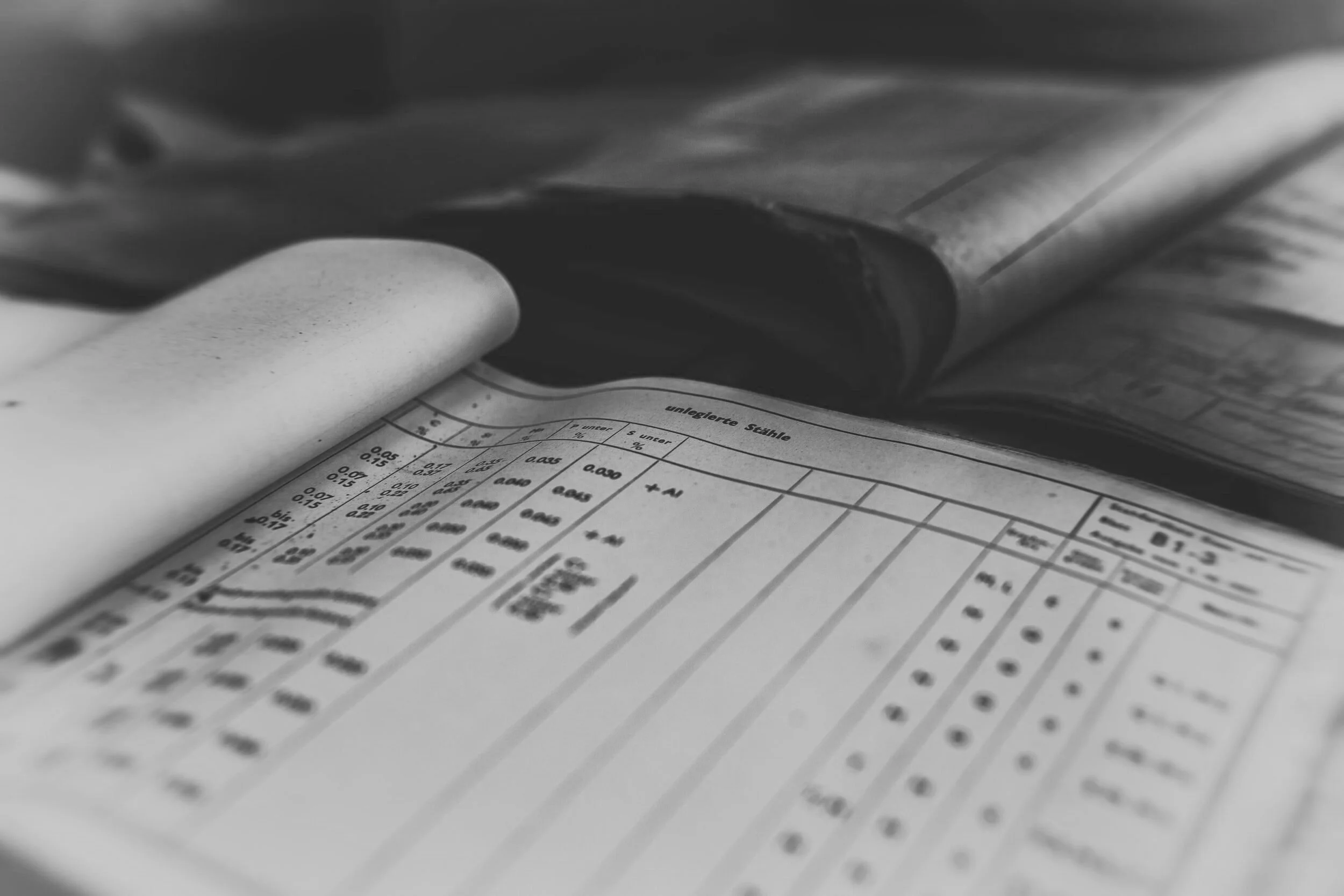
Business System Manufacturing Order
We rethought the interface for our client's business system for creating and manufacturing orders and ultimately the manufacturing order inventory pick list. Our goal was to remove unnecessary information, sort the data by how the inventory team picks the parts and surface other information that was previously invisible to the end user. This process allowed the team to put stops and warnings in place to catch issues earlier on in the client’s production process. Inventory pick lists were reduced in paper use by 75% by putting only relevant information on that document.
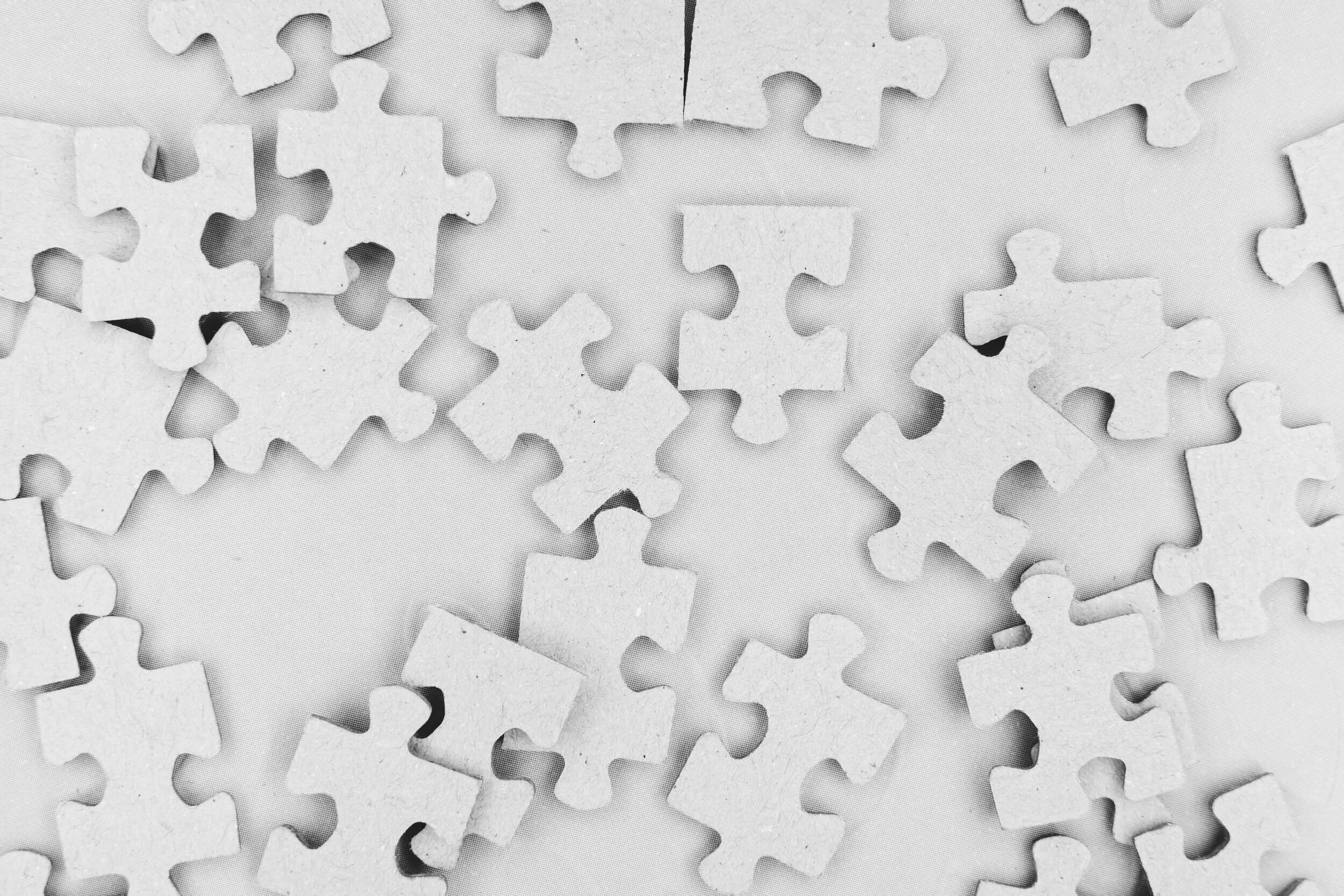
Business System Item Number
We rethought our client's business system interface and removed confusing codes that had been committed to memory. Moreover, additional safeguards were put into place to prevent errors. Removing cumbersome spreadsheets for the next number in a sequence was a game changer. We also embedded this project into the client's product configurators, allowing sales to generate their own item numbers. This consolidation of processes automates two communication steps from sales and engineering.

Universal Search Tool
We created a Universal Search tool to build a library of files that live on network drives and allow for instantaneous search results. The Universal Search tool also enables anyone to search, filter and sort any data store that the company has in any of their other business systems. Users can now make elaborate searches on their own without bothering the IT department. The Universal Search tool has also been propagated out to other projects for better search functionality in other areas of the client's data.
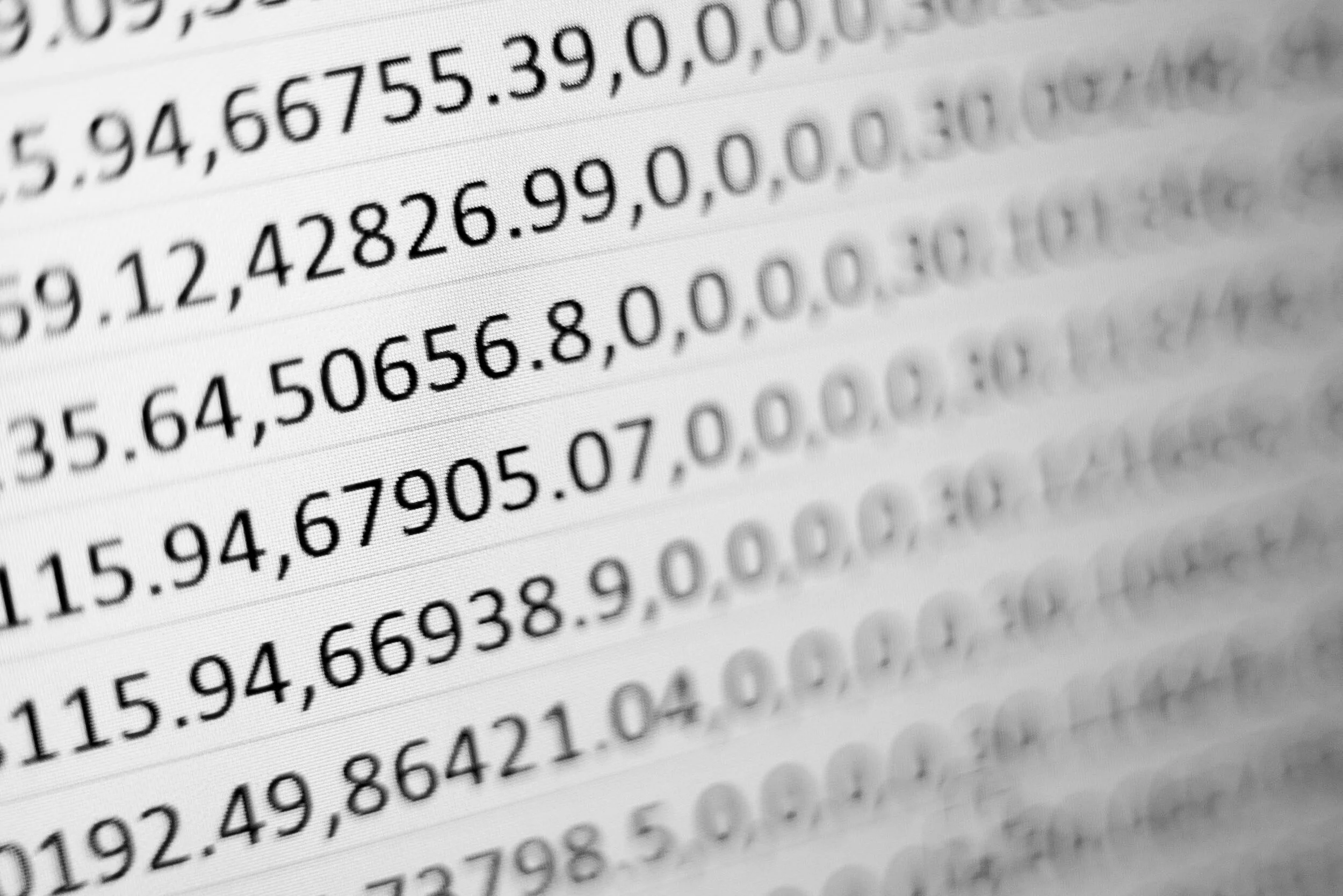
Bill of Materials (BOM) Uploads
We built a third party integration to allow a client's engineering department to upload a spreadsheet of their bills of materials out of a Solidworks Drawing and into their business system.
Their previous tool was confusing, had many steps, was prone to errors, and at times would not work at all. We decided to rewrite this functionality. Engineering now has a single step directly from Solidworks that uploads the BOM and reports back a successful or failed upload with a description of every error or warning. This has allowed the team to apply more safeguards and cover other shortcomings that may present themselves within their business system.